Low-Density Polyethylene (LDPE)
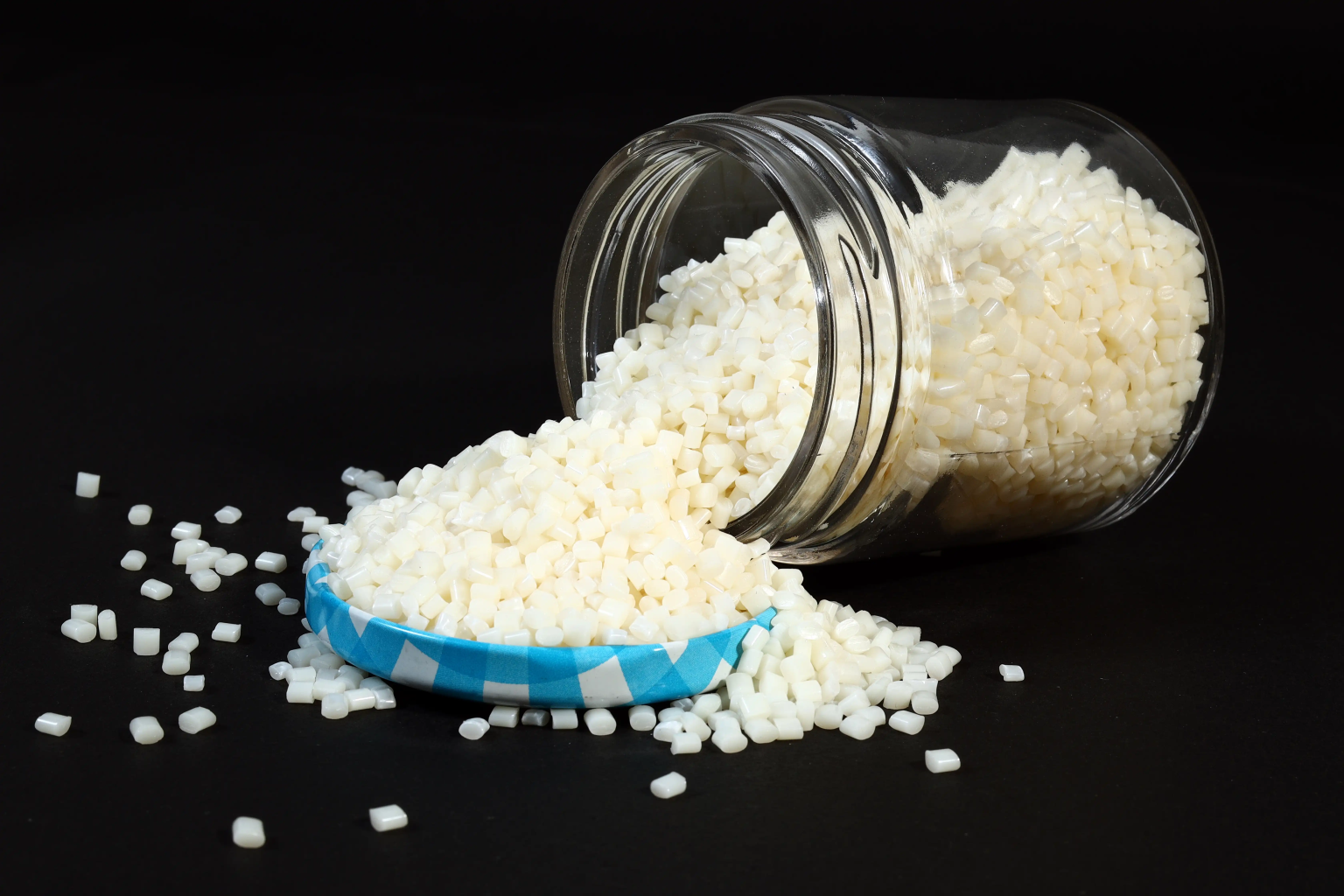
Low-density polyethylene (LDPE) is a versatile thermoplastic polymer widely used across various industries due to its distinct properties. Derived from petroleum, LDPE is produced through a polymerization process, where ethylene molecules are chemically bonded to form long, branched molecular chains. This unique structure contributes to its low density and flexibility, setting it apart from other types of polyethylene.
One of the standout characteristics of LDPE is its low density, which makes it lightweight and easy to handle. The branched molecular structure gives LDPE considerable flexibility, allowing it to be molded into thin, durable films that are commonly used in packaging. For instance, LDPE is a popular choice for creating packaging films, such as shrink wraps, as well as for manufacturing squeeze bottles.
Additionally, LDPE’s flexibility makes it suitable for products that require pliability, like plastic bags, tubing, and protective coatings for wires and cables. Its adaptability and durability are highly valued for these applications, where it must retain strength while being flexible.
LDPE’s resistance to moisture, chemicals, and UV radiation makes it a top choice for both indoor and outdoor applications. These qualities enable LDPE to withstand harsh environmental conditions, which is especially important for products exposed to the elements. For example, LDPE is often used in agricultural films, outdoor storage bags, and greenhouse covers due to its ability to resist degradation from sunlight and chemical exposure. Additionally, its high impact resistance makes it ideal for items that require a degree of toughness, such as certain toys and sporting goods. This durability helps these products maintain their shape and performance even when subjected to repeated use or impact.
Another significant advantage of LDPE is its ease of processing. The material can be readily shaped using various manufacturing techniques, including extrusion, molding, and blow molding. These methods allow LDPE to be formed into an extensive range of shapes and sizes, making it a cost-effective choice for manufacturers. LDPE’s ease of processing not only contributes to lower production costs but also allows for faster and more efficient production cycles, which is beneficial for large-scale applications, such as packaging and industrial films.
However, LDPE does have some limitations. Compared to high-density polyethylene (HDPE), LDPE is less strong and has a lower resistance to heat, which restricts its use in applications where high structural integrity or thermal stability is required. For example, LDPE is unsuitable for high-temperature environments, as it can soften or deform under intense heat. In these cases, HDPE, with its higher density and improved heat resistance, is a more appropriate choice.
Additionally, while LDPE is recyclable, it is generally less recyclable than HDPE, which can impact its sustainability profile. LDPE recycling often involves converting the material into lower-grade products, such as trash bags, plastic lumber, or irrigation piping, rather than repurposing it back into food-grade or packaging materials. Despite these challenges, efforts are being made to increase the recycling of LDPE to reduce environmental impact.
In summary, LDPE is a widely used thermoplastic known for its low density, flexibility, toughness, and resistance to moisture, chemicals, and UV radiation. These characteristics make LDPE highly valuable for packaging materials, flexible tubing, and coatings for wires and cables. While it may not be as strong or heat-resistant as HDPE, LDPE remains a popular choice for applications where lightweight durability and ease of processing are prioritized.
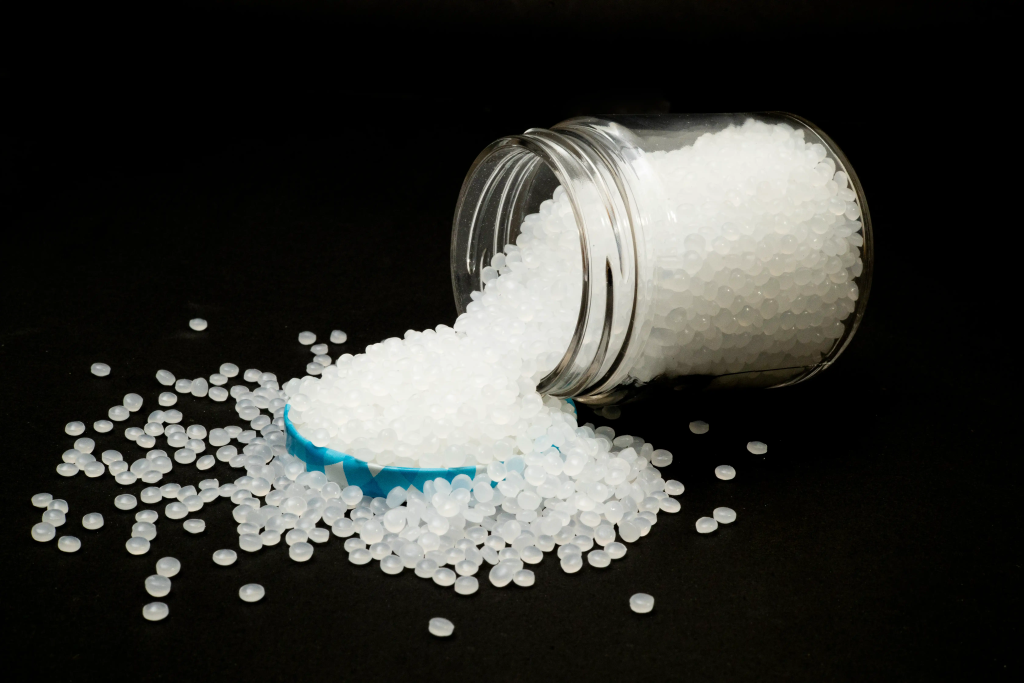
Low-density polyethylene (LDPE) is a versatile thermoplastic polymer widely used across various industries due to its distinct properties. Derived from petroleum, LDPE is produced through a polymerization process, where ethylene molecules are chemically bonded to form long, branched molecular chains. This unique structure contributes to its low density and flexibility, setting it apart from other types of polyethylene.
One of the standout characteristics of LDPE is its low density, which makes it lightweight and easy to handle. The branched molecular structure gives LDPE considerable flexibility, allowing it to be molded into thin, durable films that are commonly used in packaging. For instance, LDPE is a popular choice for creating packaging films, such as shrink wraps, as well as for manufacturing squeeze bottles. Additionally, LDPE’s flexibility makes it suitable for products that require pliability, like plastic bags, tubing, and protective coatings for wires and cables. Its adaptability and durability are highly valued for these applications, where it must retain strength while being flexible.
LDPE’s resistance to moisture, chemicals, and UV radiation makes it a top choice for both indoor and outdoor applications. These qualities enable LDPE to withstand harsh environmental conditions, which is especially important for products exposed to the elements. For example, LDPE is often used in agricultural films, outdoor storage bags, and greenhouse covers due to its ability to resist degradation from sunlight and chemical exposure. Additionally, its high impact resistance makes it ideal for items that require a degree of toughness, such as certain toys and sporting goods. This durability helps these products maintain their shape and performance even when subjected to repeated use or impact.
Another significant advantage of LDPE is its ease of processing. The material can be readily shaped using various manufacturing techniques, including extrusion, molding, and blow molding. These methods allow LDPE to be formed into an extensive range of shapes and sizes, making it a cost-effective choice for manufacturers. LDPE’s ease of processing not only contributes to lower production costs but also allows for faster and more efficient production cycles, which is beneficial for large-scale applications, such as packaging and industrial films.
However, LDPE does have some limitations. Compared to high-density polyethylene (HDPE), LDPE is less strong and has a lower resistance to heat, which restricts its use in applications where high structural integrity or thermal stability is required. For example, LDPE is unsuitable for high-temperature environments, as it can soften or deform under intense heat. In these cases, HDPE, with its higher density and improved heat resistance, is a more appropriate choice.
Additionally, while LDPE is recyclable, it is generally less recyclable than HDPE, which can impact its sustainability profile. LDPE recycling often involves converting the material into lower-grade products, such as trash bags, plastic lumber, or irrigation piping, rather than repurposing it back into food-grade or packaging materials. Despite these challenges, efforts are being made to increase the recycling of LDPE to reduce environmental impact.
In summary, LDPE is a widely used thermoplastic known for its low density, flexibility, toughness, and resistance to moisture, chemicals, and UV radiation. These characteristics make LDPE highly valuable for packaging materials, flexible tubing, and coatings for wires and cables. While it may not be as strong or heat-resistant as HDPE, LDPE remains a popular choice for applications where lightweight durability and ease of processing are prioritized.
Benefits of Low-Density Polyethylene (LDPE)

High Impact Resistance

Lightweight

Electrical Insulation
One stop solution for polymers
Supplying high-quality polymers to fuel your business success!
Get in touch with us today to discover more about our premium polymer supplies!