Polycarbonate (PC)
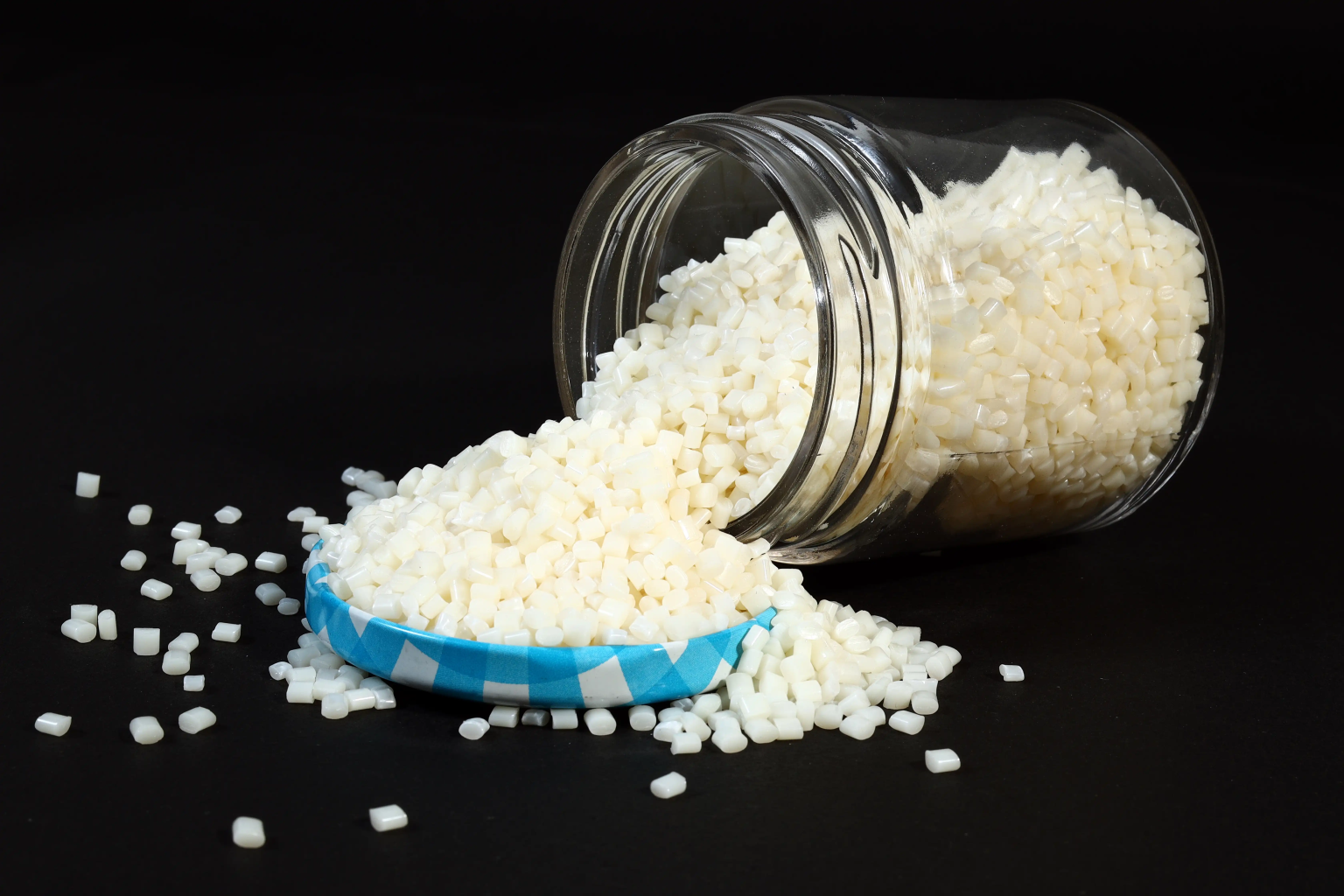
Polycarbonate (PC) is a unique and versatile thermoplastic polymer known for its exceptional strength, transparency, and durability. As an amorphous polymer, PC lacks a highly ordered structure, which gives it excellent optical clarity and makes it suitable for a wide array of applications where visibility or transparency is essential. Commonly, polycarbonate is used in products such as safety glasses, optical lenses, automotive components, electronic housings, and construction materials, demonstrating its adaptability across industries.
The production of polycarbonate involves a chemical reaction between bisphenol A and phosgene, resulting in a process called interfacial polymerization. This method creates long, robust molecular chains that contribute to PC’s outstanding mechanical properties. The resulting material is a strong, lightweight polymer that can be molded easily into various shapes and sizes,
allowing manufacturers to produce complex, custom parts without compromising the material’s strength or impact resistance.
One of polycarbonate’s defining attributes is its remarkable impact resistance, which makes it ideal for applications where durability and the ability to withstand physical forces are critical. For instance, PC is frequently chosen for the production of protective gear like safety glasses and face shields, as it can absorb impact energy and resist shattering, providing effective protection in high-risk environments. Additionally, PC’s lightweight nature combined with its high strength makes it an excellent choice for automotive parts, where a balance between durability and weight reduction is important to improve vehicle efficiency and performance.
In terms of optical properties, polycarbonate is highly valued for its clarity, which is why it’s often used in applications requiring transparency, such as electronic displays, LED lights, and glazing materials. Its transparency allows it to serve as a reliable alternative to glass in many applications, offering a lightweight, shatter-resistant option with similar visual properties. This optical clarity has also led to PC’s widespread use in the production of lenses and light fixtures, where clear, uninterrupted vision is crucial.
Beyond its physical and optical properties, polycarbonate exhibits good electrical insulation, making it suitable for various electrical and electronic applications. Its insulating qualities, combined with its resistance to heat, make PC a preferred material for electrical housings and components that need to endure both mechanical and thermal stress without compromising safety.
Despite its numerous advantages, PC does have some limitations. It is relatively more expensive than other thermoplastics, which can make it less desirable for applications where cost is a primary concern. Additionally, polycarbonate is somewhat prone to scratching, which can reduce its clarity over time, especially in applications where the surface is frequently exposed to abrasive conditions. It can also discolor and become brittle when exposed to prolonged UV radiation, limiting its use outdoors unless treated with UV-resistant coatings.
Polycarbonate also has a moderate thermal stability compared to some high-heat thermoplastics. While it can endure elevated temperatures, excessive heat exposure can lead to degradation, and, if burned, PC can emit potentially harmful fumes. For applications requiring extreme heat resistance, polycarbonate may need to be modified or blended with additives to improve performance.
To enhance its properties further, polycarbonate can be reinforced or blended with other materials. For example, adding glass fibers to polycarbonate creates a glass-reinforced polycarbonate (GRP), a material with increased stiffness and strength, ideal for industrial applications that demand even greater durability. Other additives can be used to improve UV stability, scratch resistance, or heat tolerance, allowing polycarbonate to be tailored for specific uses.
In summary, polycarbonate (PC) is an exceptionally useful material, particularly valued for its impact resistance, transparency, and electrical insulation properties. While it has limitations in terms of UV stability, heat tolerance, and cost, polycarbonate’s versatility and strength make it an ideal choice for a wide range of applications, especially those requiring a combination of toughness and optical clarity. By blending PC with other polymers or reinforcing it with fibers, its performance can be enhanced to meet the specific needs of various industries, making it one of the most adaptable and widely used thermoplastics today.
The production of polycarbonate involves a chemical reaction between bisphenol A and phosgene, resulting in a process called interfacial polymerization. This method creates long, robust molecular chains that contribute to PC’s outstanding mechanical properties. The resulting material is a strong, lightweight polymer that can be molded easily into various shapes and sizes, allowing manufacturers to produce complex, custom parts without compromising the material’s strength or impact resistance.
One of polycarbonate’s defining attributes is its remarkable impact resistance, which makes it ideal for applications where durability and the ability to withstand physical forces are critical. For instance, PC is frequently chosen for the production of protective gear like safety glasses and face shields, as it can absorb impact energy and resist shattering, providing effective protection in high-risk environments. Additionally, PC’s lightweight nature combined with its high strength makes it an excellent choice for automotive parts, where a balance between durability and weight reduction is important to improve vehicle efficiency and performance.
In terms of optical properties, polycarbonate is highly valued for its clarity, which is why it’s often used in applications requiring transparency, such as electronic displays, LED lights, and glazing materials. Its transparency allows it to serve as a reliable alternative to glass in many applications, offering a lightweight, shatter-resistant option with similar visual properties. This optical clarity has also led to PC’s widespread use in the production of lenses and light fixtures, where clear, uninterrupted vision is crucial.
Beyond its physical and optical properties, polycarbonate exhibits good electrical insulation, making it suitable for various electrical and electronic applications. Its insulating qualities, combined with its resistance to heat, make PC a preferred material for electrical housings and components that need to endure both mechanical and thermal stress without compromising safety.
Despite its numerous advantages, PC does have some limitations. It is relatively more expensive than other thermoplastics, which can make it less desirable for applications where cost is a primary concern. Additionally, polycarbonate is somewhat prone to scratching, which can reduce its clarity over time, especially in applications where the surface is frequently exposed to abrasive conditions. It can also discolor and become brittle when exposed to prolonged UV radiation, limiting its use outdoors unless treated with UV-resistant coatings.
Polycarbonate also has a moderate thermal stability compared to some high-heat thermoplastics. While it can endure elevated temperatures, excessive heat exposure can lead to degradation, and, if burned, PC can emit potentially harmful fumes. For applications requiring extreme heat resistance, polycarbonate may need to be modified or blended with additives to improve performance.
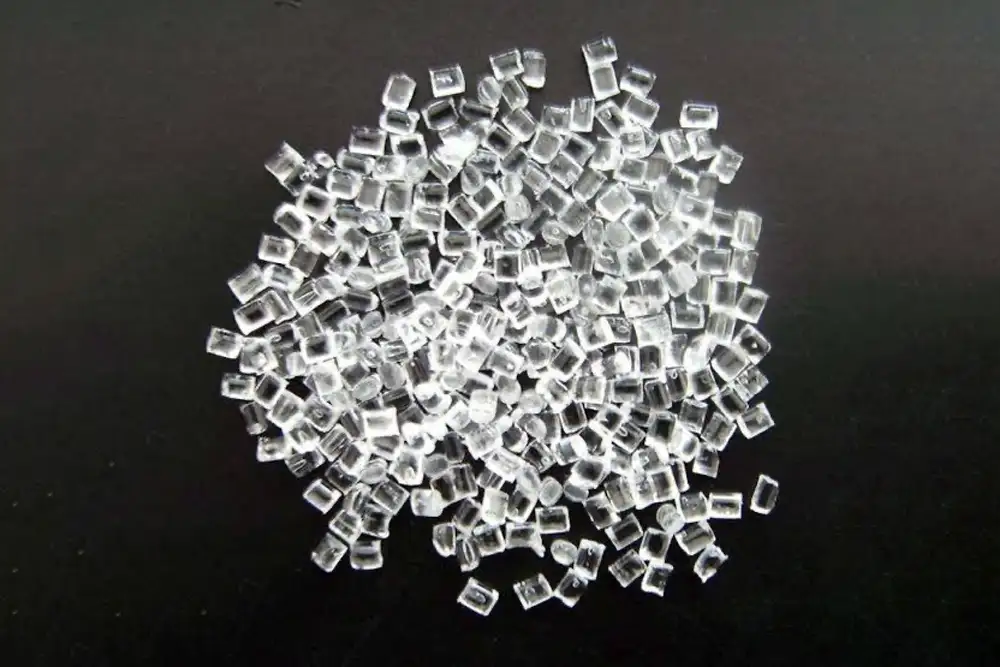
Polycarbonate (PC) is a unique and versatile thermoplastic polymer known for its exceptional strength, transparency, and durability. As an amorphous polymer, PC lacks a highly ordered structure, which gives it excellent optical clarity and makes it suitable for a wide array of applications where visibility or transparency is essential. Commonly, polycarbonate is used in products such as safety glasses, optical lenses, automotive components, electronic housings, and construction materials, demonstrating its adaptability across industries.
The production of polycarbonate involves a chemical reaction between bisphenol A and phosgene, resulting in a process called interfacial polymerization. This method creates long, robust molecular chains that contribute to PC’s outstanding mechanical properties. The resulting material is a strong, lightweight polymer that can be molded easily into various shapes and sizes, allowing manufacturers to produce complex, custom parts without compromising the material’s strength or impact resistance.
One of polycarbonate’s defining attributes is its remarkable impact resistance, which makes it ideal for applications where durability and the ability to withstand physical forces are critical. For instance, PC is frequently chosen for the production of protective gear like safety glasses and face shields, as it can absorb impact energy and resist shattering, providing effective protection in high-risk environments. Additionally, PC’s lightweight nature combined with its high strength makes it an excellent choice for automotive parts, where a balance between durability and weight reduction is important to improve vehicle efficiency and performance.
In terms of optical properties, polycarbonate is highly valued for its clarity, which is why it’s often used in applications requiring transparency, such as electronic displays, LED lights, and glazing materials. Its transparency allows it to serve as a reliable alternative to glass in many applications, offering a lightweight, shatter-resistant option with similar visual properties. This optical clarity has also led to PC’s widespread use in the production of lenses and light fixtures, where clear, uninterrupted vision is crucial.
Beyond its physical and optical properties, polycarbonate exhibits good electrical insulation, making it suitable for various electrical and electronic applications. Its insulating qualities, combined with its resistance to heat, make PC a preferred material for electrical housings and components that need to endure both mechanical and thermal stress without compromising safety.
Despite its numerous advantages, PC does have some limitations. It is relatively more expensive than other thermoplastics, which can make it less desirable for applications where cost is a primary concern. Additionally, polycarbonate is somewhat prone to scratching, which can reduce its clarity over time, especially in applications where the surface is frequently exposed to abrasive conditions. It can also discolor and become brittle when exposed to prolonged UV radiation, limiting its use outdoors unless treated with UV-resistant coatings.
Polycarbonate also has a moderate thermal stability compared to some high-heat thermoplastics. While it can endure elevated temperatures, excessive heat exposure can lead to degradation, and, if burned, PC can emit potentially harmful fumes. For applications requiring extreme heat resistance, polycarbonate may need to be modified or blended with additives to improve performance.
To enhance its properties further, polycarbonate can be reinforced or blended with other materials. For example, adding glass fibers to polycarbonate creates a glass-reinforced polycarbonate (GRP), a material with increased stiffness and strength, ideal for industrial applications that demand even greater durability. Other additives can be used to improve UV stability, scratch resistance, or heat tolerance, allowing polycarbonate to be tailored for specific uses.
In summary, polycarbonate (PC) is an exceptionally useful material, particularly valued for its impact resistance, transparency, and electrical insulation properties. While it has limitations in terms of UV stability, heat tolerance, and cost, polycarbonate’s versatility and strength make it an ideal choice for a wide range of applications, especially those requiring a combination of toughness and optical clarity. By blending PC with other polymers or reinforcing it with fibers, its performance can be enhanced to meet the specific needs of various industries, making it one of the most adaptable and widely used thermoplastics today.
The production of polycarbonate involves a chemical reaction between bisphenol A and phosgene, resulting in a process called interfacial polymerization. This method creates long, robust molecular chains that contribute to PC’s outstanding mechanical properties. The resulting material is a strong, lightweight polymer that can be molded easily into various shapes and sizes, allowing manufacturers to produce complex, custom parts without compromising the material’s strength or impact resistance.
One of polycarbonate’s defining attributes is its remarkable impact resistance, which makes it ideal for applications where durability and the ability to withstand physical forces are critical. For instance, PC is frequently chosen for the production of protective gear like safety glasses and face shields, as it can absorb impact energy and resist shattering, providing effective protection in high-risk environments. Additionally, PC’s lightweight nature combined with its high strength makes it an excellent choice for automotive parts, where a balance between durability and weight reduction is important to improve vehicle efficiency and performance.
In terms of optical properties, polycarbonate is highly valued for its clarity, which is why it’s often used in applications requiring transparency, such as electronic displays, LED lights, and glazing materials. Its transparency allows it to serve as a reliable alternative to glass in many applications, offering a lightweight, shatter-resistant option with similar visual properties. This optical clarity has also led to PC’s widespread use in the production of lenses and light fixtures, where clear, uninterrupted vision is crucial.
Beyond its physical and optical properties, polycarbonate exhibits good electrical insulation, making it suitable for various electrical and electronic applications. Its insulating qualities, combined with its resistance to heat, make PC a preferred material for electrical housings and components that need to endure both mechanical and thermal stress without compromising safety.
Despite its numerous advantages, PC does have some limitations. It is relatively more expensive than other thermoplastics, which can make it less desirable for applications where cost is a primary concern. Additionally, polycarbonate is somewhat prone to scratching, which can reduce its clarity over time, especially in applications where the surface is frequently exposed to abrasive conditions. It can also discolor and become brittle when exposed to prolonged UV radiation, limiting its use outdoors unless treated with UV-resistant coatings.
Polycarbonate also has a moderate thermal stability compared to some high-heat thermoplastics. While it can endure elevated temperatures, excessive heat exposure can lead to degradation, and, if burned, PC can emit potentially harmful fumes. For applications requiring extreme heat resistance, polycarbonate may need to be modified or blended with additives to improve performance.
Benefits of Polycarbonate (PC)

High Impact Resistance

Lightweight

Recyclable
One stop solution for polymers
Supplying high-quality polymers to fuel your business success!
Get in touch with us today to discover more about our premium polymer supplies!